Kõik vedrutraadi kohta

Vedrutraat (PP) on metallisulamitest valmistatud ülitugev toode. Seda kasutatakse surve-, väände-, venitusvedrude vabastamisel; erinevat tüüpi konksud, teljed, juuksenõelad, klaverikeeled ja muud vedruomadustega osad.
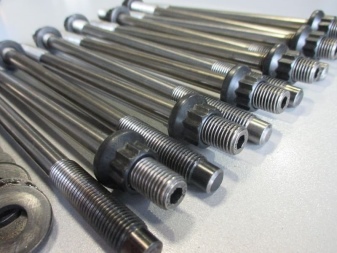
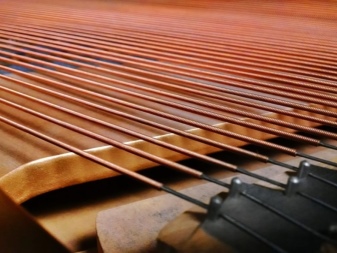
Omadused ja nõuded
Kõige populaarsem läbimõõt on 6-8 millimeetrit. Vedrutraadi valmistamiseks kasutatakse terasvarda. Tehnilised nõuded kehtestatakse vastavalt standarditele GOST 14963-78 või GOST 9389-75. Mõnikord on lubatud kõrvalekalded normidest vedrutraadi nõuetest. Näiteks võib kliendi soovil mangaani kogus koostises muutuda, kuid ainult siis, kui valmistamisel ei kasutatud kroomi ja niklit.
Valmistoodete osalise või täieliku hävimise vältimiseks näeb GOST ette traatvõrgu ideaalse pinna ilma defektideta.
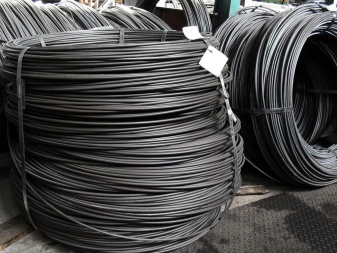
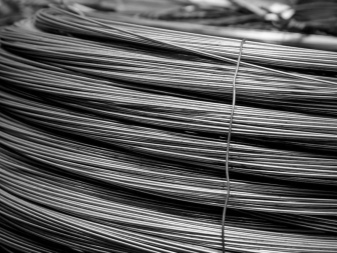
Töö ajal tekib koormus kohtadesse, mis ei ole vigade suhtes vastupidavad. Seetõttu testitakse kõiki tooraineid enne vedrude valmistamist.
Vedruvõrgu tugevus on otseselt seotud läbimõõdu suurusega, väikese läbimõõdu tugevus on palju suurem. Näiteks 0,2-1 mm ristlõike suurus on peaaegu kaks korda tugevam kui 8 mm ristlõikega traat.Valmis vedrutraadi vabastamise vorm võib olla poolide, mähiste (lubatud kaal 80–120 kilogrammi) ja lahtrite (500–800 kilogrammi) kujul.
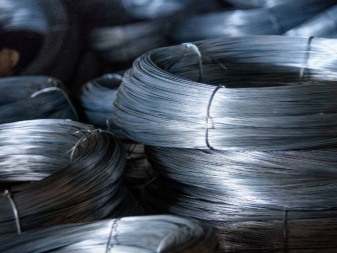
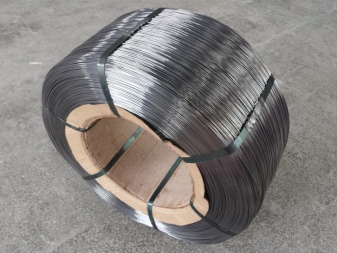
Tootmine
Vastavalt kehtestatud GOST-reeglitele luuakse traat esialgsete toorikute tõmbamise või tõmbamisega läbi aukude, mis on paigutatud ristlõike läbimõõdu vähenemise järjekorras. Tõmbetugevuse suurendamiseks viiakse lõpus läbi termiline karastamine. Joonistamisel paigaldatakse masina viimasele väljalaskeavale spetsiaalne kalibreerimisvorm - stants. See on määratud juhuks, kui materjal peab olema juba kalibreeritud ja sellel ei tohi olla defekte.
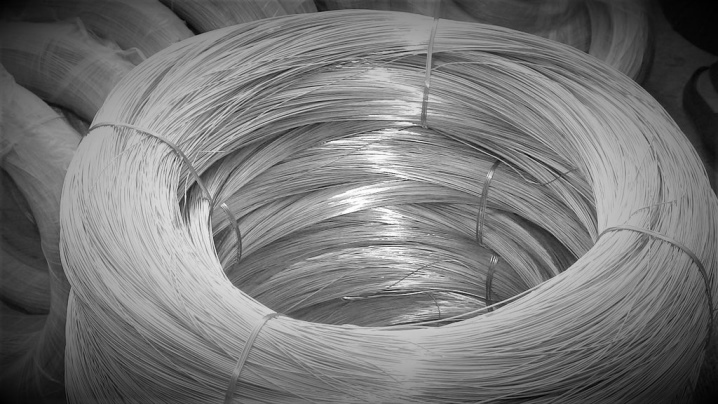
Traadi valmistamiseks kasutatavate toorainete peamised omadused on materjali elastsus ja voolavus. Elastsuse suurenemine saavutatakse sulami karastamise teel õlis, mille temperatuur võib olla 820-870 C.
Järgmiseks järgneb traadi karastamine temperatuuril 400-480 C. Kanga kõvadus on 35-45 ühikut (1300-1600 kilogrammi tasapinna 1 ruutmillimeetri kohta). Sellise tehnilise omaduse, nagu koormuse summutamine, parandamiseks kasutatakse süsinikku või kõrglegeeritud terast. Tavaliselt toodavad tootjad seda sulamiklassidest - 50HFA, 50HGFA, 55HGR, 55S2, 60S2, 60S2A, 60S2N2A, 65G, 70SZA, U12A, 70G.
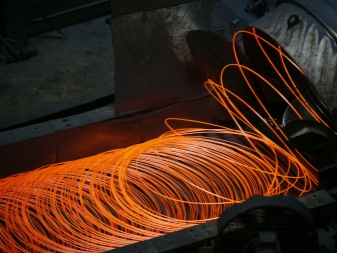
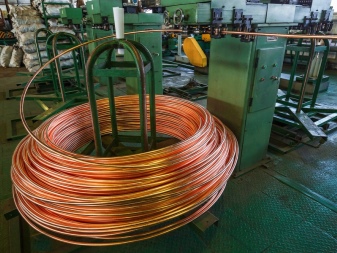
Vaata ülevaadet
Keemilise koostise järgi jaguneb terastraat süsinikuks ja legeeritud. Esimesed jagunevad madala süsinikusisaldusega süsinikusisaldusega kuni 0,25%, keskmise süsinikusisaldusega süsinikusisaldusega 0,25–0,6% ja suure süsinikusisaldusega süsinikusisaldusega 0,6–2,0%. Eraldi sort on roostevaba teras või korrosioonikindel. Sellised omadused saavutatakse, lisades kompositsioonile legeerivaid komponente - nikli (9-12%) ja kroomi (13-27%).Olenevalt algsest toorainest võib traadi lõpptulemus olla tume või heledamaks muutunud, pehme või kõva.
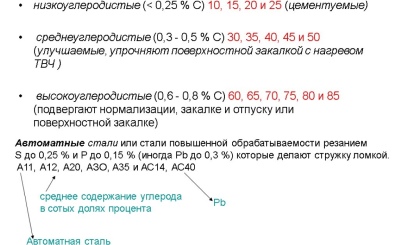
Sellist sorti nagu mäluga terastraat on võimatu mitte märkida - kompositsioonis sisalduv titaan ja neodüüm annavad sellele ebatavalised omadused.
Kui toodet mõne aja pärast sirgeks ajada ja tulel kuumutada, taastub traat oma esialgse kujuga. Vastavalt mehaanilistele omadustele jaguneb vedrutraat järgmisteks osadeks:
- klassid - 1, 2, 2A ja 3;
- kaubamärgid - A, B, C;
- vastupidavus koormustele - väga koormatud ja tugevalt koormatud;
- rakenduskoormustele - kokkusurumine, painutamine, pingutus ja vääne;
- sektsiooni läbimõõdu suurus - võimalik on ka ümmargune ja ovaalne, ruudu- ja ristkülikukujuline, kuusnurkne ja trapetsikujuline;
- jäikustüüp — muutuv jäikus ja konstantne jäikus.
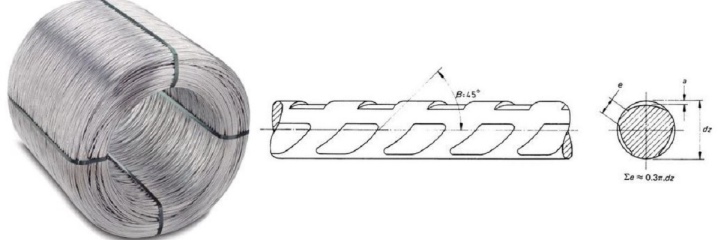
Tootmistäpsuse osas võib traat olla kõrgendatud täpsusega - seda kasutatakse keerukate mehhanismide valmistamisel ja kokkupanemisel, normaalse täpsusega - seda kasutatakse vähem keerukate mehhanismide valmistamisel ja kokkupanemisel.
Kus seda rakendatakse?
Vedrude tootmine on külm ja kuum tehnika. Külmmähimiseks kasutatakse spetsiaalseid vedrumähismasinaid ja -masinaid. Traat peab olema süsinikterasest, sest viimane osa ei kõvene. Venemaal kasutatakse külmmeetodit sagedamini, kuna see pole nii kallis ja kulukas.
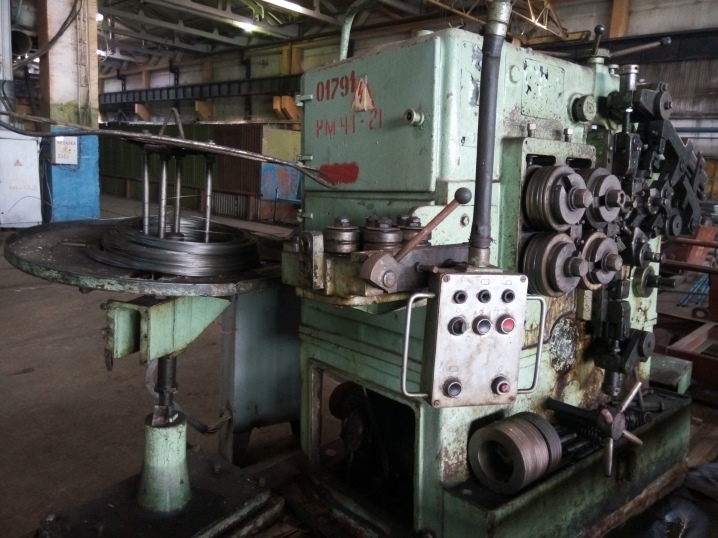
Külmmähisseadmed on varustatud kahe peavõlliga, millest üks reguleerib pinget, teine määrab mähise suuna.
Protsessi kirjeldus.
- Vedrutraat on tööks ette valmistatud, defektide suhtes kontrollitud.
- Traadileht on keermestatud läbi pidurisadulas oleva kronsteini ja ots kinnitatakse klambriga raami külge.
- Ülemine võll reguleerib pinget.
- Kerimisrull on sisse lülitatud (selle kiirus sõltub traadi läbimõõdust).
- Lint lõigatakse ära, kui soovitud pöörete arv on saavutatud.
- Viimane etapp on valmisosa mehaaniline ja kuumtöötlus.
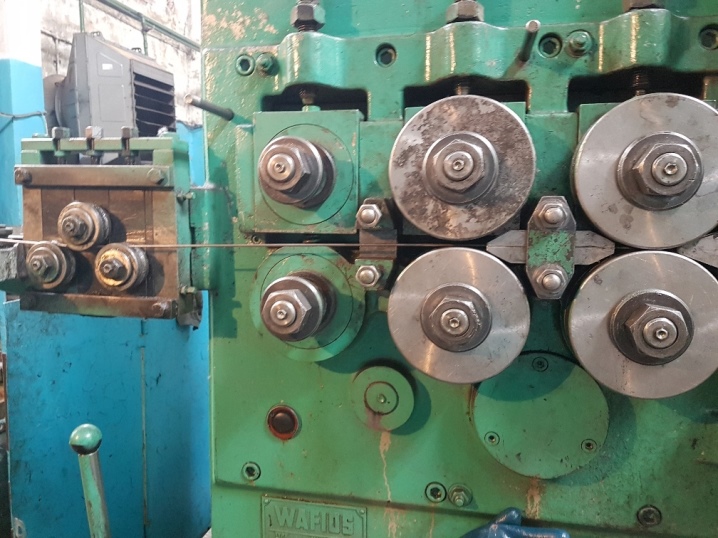
Kuuma meetodiga saab toota ainult osi, mille ristlõike läbimõõt on 1 sentimeeter. Kerimise ajal toimub kiire ja ühtlane kuumenemine. Protsess näeb välja selline.
- Läbi hoidiku surutakse kuumaks kuumutatud traadileht ja selle otsad kinnitatakse klambritega.
- Ülemine rull määrab pinge.
- Pöörlemiskiirust reguleeritakse (oleneb ka läbimõõdust), masin lülitatakse sisse.
- Pärast töödeldava detaili eemaldamist.
- Edasi tuleb termiline karastamine – jahutamine õlilahuses.
- Valmis detaili töötlemine ja korrosioonivastase segu pealekandmine.
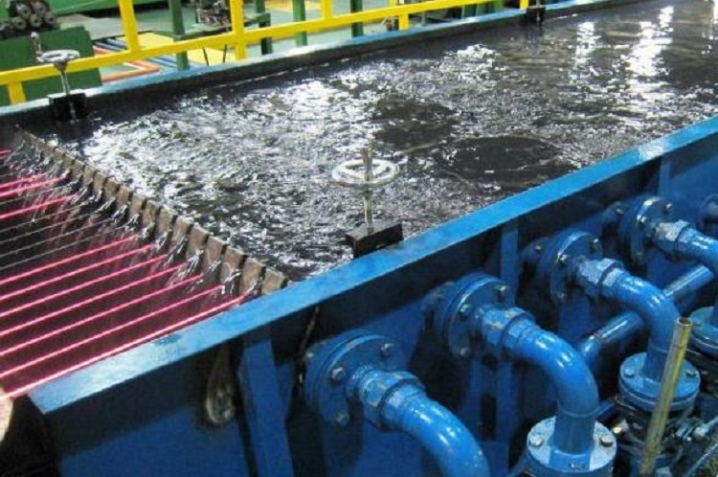
Kuumkerimismeetodil vedru tükkideks lõikamist ei võimaldata, kui soovitud suurus on juba saavutatud, st kerimine toimub kogu võrgu pikkuses. Pärast seda lõigatakse see soovitud pikkusega tükkideks. Selle meetodi puhul on detaili sisemise pinge eemaldamiseks vaja viimast kuumtöötlust. Soovitatav on töötada õlilahusega, mitte veega, et teras ei praguneks kõvenemisel.
Kuidas vedrutraat välja näeb, vaata allpool.
Kommentaari saatmine õnnestus.